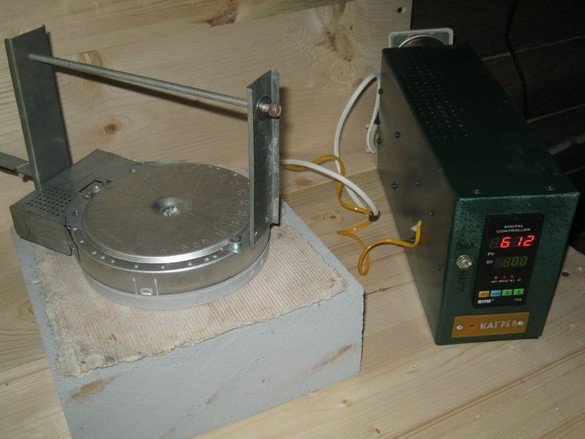
A fusão (por fusão do fusível - sinterização, fundição) é relativamente nova bordado e como é agora, nasceu em 1990. Aparentemente, a fabricação de um vitral “sinterizado” tornou-se possível com o advento de vitrais com KTP igual (coeficiente de expansão térmica). É feito assim - em uma base de vidro, é apresentado um padrão de pedaços de vidro coloridos e suas bordas, na maioria dos casos, não requerem ajuste e processamento precisos, corte e corte de vidro suficientes pinças especiais. A pré-forma montada é colocada em um forno especial e aquecida à temperatura em que o vidro derrete.
O vitral resultante parece muito peculiar - bordas arredondadas e suaves, cada elemento se assemelha a uma espécie de doce derretido. Com um pouco de habilidade artística, temos aparelhos muito interessantes. Além disso, aqui você pode usar todo um arsenal de técnicas - use papel de metal, serragem, arame, estênceis para eles, técnicas de esmalte cloisonné, aplique tintas de queima em vidro e cerâmica, produtos químicos que produzam bolhas dentro do vidro. O forno de fusão também permite a moldagem de dobragem de vidro plano. Os aparelhos finalizados podem ser combinados com os métodos de "baixa temperatura", em grandes vitrais. Em uma palavra - um abismo de oportunidades para a criatividade.
O vitral com a mesma CTE, como muitos materiais para fusão, é caro, no entanto, o artigo mais caro para dominar essa técnica é, naturalmente, o forno. Um forno para fusão de copos é bastante incomum, sua forma é ditada pela tecnologia de sinterização - uma mesa plana, na qual é conveniente colocar uma folha de vidro em branco, uma tampa articulada com aquecedores. Em geral, parece uma mala, em alguns, existem até fixadores.
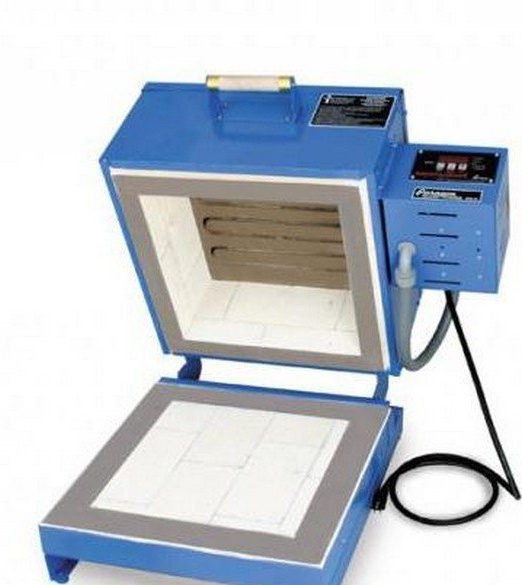
Os fornos de mufla - com um aquecedor no topo da câmara da mufla, não são usados - após o aquecimento do vidro até o ponto de fusão, o produto deve ser resfriado rapidamente até a temperatura de recozimento, enquanto os fornos costumam ser levemente abertos. É difícil uma queda rápida de temperatura na mufla - a inércia térmica é muito alta e é inconveniente colocar os espaços em branco na câmara.
Fornos para fusão, existem tamanhos muito diferentes, respectivamente - capacidades. Com aquecedores de um pequeno fogão, a fiação doméstica pode lidar muito bem.
Sinterização de vidro "por não ser caro".
Você pode se dedicar a esse negócio interessante sem gastar grandes somas - para iniciantes, existe uma versão original do Ali Express - cadinhos especiais para o microondas. É um cadinho refratário com revestimento de grafite por dentro. O revestimento é aquecido em ondas de microondas e aquece o vidro com radiação. Há uma virtude, mas uma quantidade justa - custo. No momento da escrita, o cadinho custava de 2 a 4 mil rublos. dependendo do tamanho.
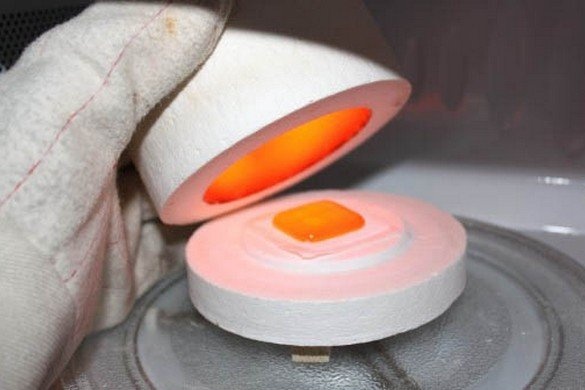
As desvantagens de uma opção tão simples, como sempre, são as massas. A temperatura pode ser controlada apenas visualmente, "a olho nu", o recozimento controlado para aliviar as tensões internas é impossível. Tamanho pequeno - apenas para jóias, a incapacidade de usar metais. Como regra, tendo selecionado experimentalmente o modo de sinterização e consumido os fragmentos de vidro incluídos no kit, são lançadas a ocupação e o cadinho.
Um forno elétrico especializado, é claro, é muito mais perfeito, no entanto, o menor - 200x200 mm, custa 35 mil rublos. É claro - apenas refratários, um controlador com perfil térmico, quartzo e tubos de cerâmica para aquecedores, montagem novamente ... Tendo uma oficina ou garagem, um pouco de habilidades em metal e experiência com eletricidade, é bem possível montar você mesmo esse forno, gastando menos da metade do custo de materiais , mas o que fazer com moradores sem cavalos e sem garras da "selva de concreto"?
Ideia.
A idéia de um forno de fusão extremamente simples e barato de características "intermediárias" pertence à camarada "Ilya MSU", do fórum do metal. O forno é pequeno, mas já é possível assar o copo, muito mais sério do que os pingentes no microondas. Você pode usar arame, papel alumínio e todo o arsenal de técnicas de fusão. Aquecedor de resistência elétrica na tampa, termopar com um simples controlador de temperatura. Baixa, mesmo para o poder de um apartamento, a capacidade de fabricar na cozinha elementos e peças baratas e difundidas. O design não contém refratários especializados para alta temperatura.
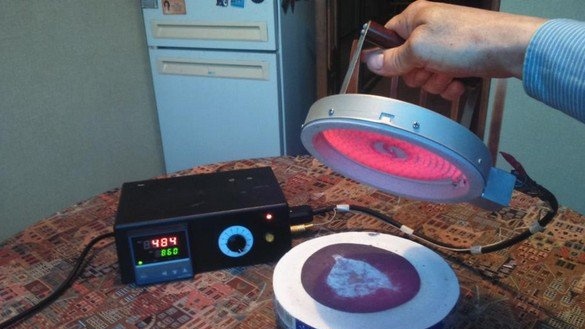
Como tampa superior do forno, é usada uma parte de um fogão elétrico com superfície vitrocerâmica - um queimador. Possui um invólucro metálico forrado com refratário fibroso, no qual são formadas protrusões especiais da fita do aquecedor. O queimador é complementado por uma alça e um termopar conectado a um controlador simples. Como base, foi utilizada uma lata plana cheia de gesso.
Versão própria de um fogão simples.
Eu tenho dois queimadores de segunda mão com um diâmetro interno de trabalho de 140 mm, com um termostato mecânico em uma caixa de metal (existem opções com um tubo de quartzo).
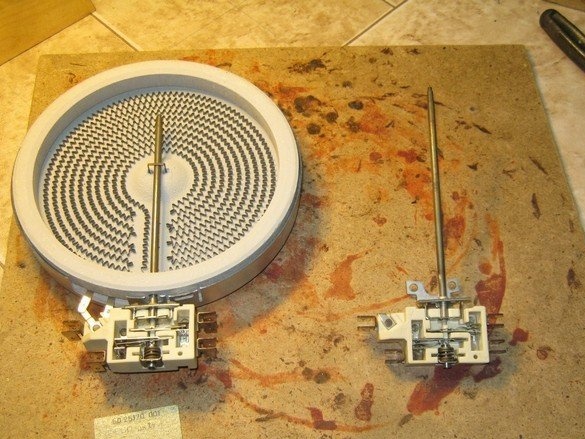
O que foi usado no trabalho.
Ferramentas, dispositivos, equipamentos.
Um conjunto de ferramentas comuns de bancada de tamanho médio, um quebra-cabeças de jóias com acessórios, uma rebarbadora pequena, uma chave de fenda ou uma furadeira elétrica. Um conjunto de ferramentas de fiação, um ferro de solda de 40 W para fiação, maior - 60 ... 80 W - para solda estrutural. Ferramenta de marcação. Ferramenta útil para instalar rebites cegos, construir secador de cabelo.
Materiais
Além dos queimadores, eles precisavam de amianto em chapa, tijolos de concreto com espuma, fios diferentes, um termopar, termotubos, grampos de nylon. Foi utilizada uma unidade de controle pronta para um forno mufla (ou um controlador + relé de estado sólido + radiador + gabinete). Resistor de extinção de potência adequada (aquecedor a óleo). Um pouco de fixadores de aço galvanizado.
Os contatos do termostato da placa de aquecimento foram fechados e soldados com força, solda de estanho-cobre nos terminais de saída, fios de isolamento de silicone foram soldados. Ao lado do termostato, um orifício foi perfurado na cavidade interna, um termopar cromo-alumínio (tipo K) foi introduzido, a partir de um multímetro. À sonda do termostato padrão, o termopar conectou várias voltas de fio de nicromo.
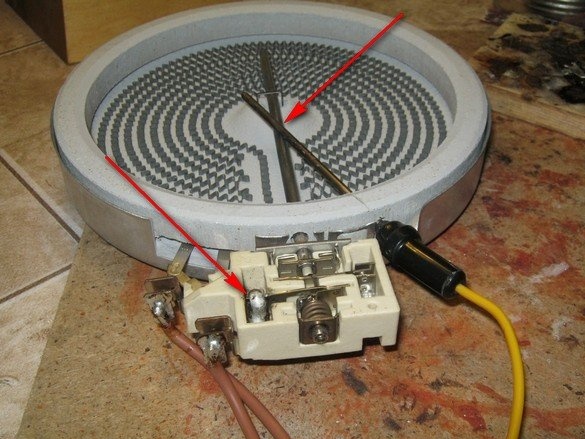
Tampa de estanho - de fato, acabou sendo o elemento mais difícil do meu forno. É soldado a partir de aço galvanizado de 0,5 mm, cobre-estanho-cobre (o ponto de fusão é superior ao das soldas de chumbo). Ácido de solda por fluxo (cloreto de zinco), ferro de solda a 60 watts.Peças complexas foram serradas com um quebra-cabeças de jóias, cortes retos - com uma tesoura para metais. Linhas curvas foram marcadas assim - o pedaço de ferro foi colocado no lugar certo e, com um par de bússolas, com uma agulha no centro do queimador, desenhei o raio necessário para o arco.


Soldado por dentro, principalmente para estética. Em frente aos terminais de “facas” do termostato padrão do queimador, com fios soldados a eles, fizeram orifícios de ventilação (acima e abaixo) na carcaça para que eles fossem resfriados por uma corrente de ar e a solda não derretesse.
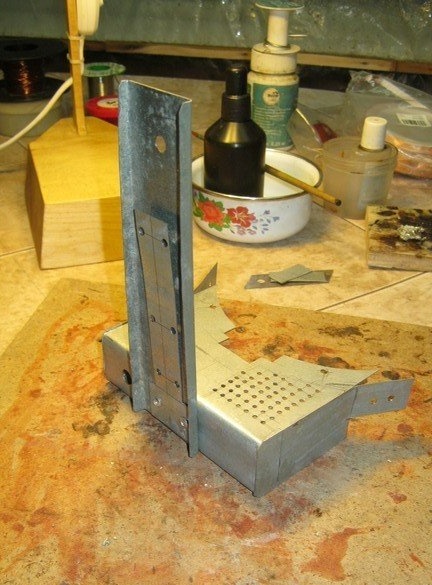
Sobre a borda da caixa, decidi prender e um dos suportes da alça, com os mesmos prendedores, prendeu um suporte aos fios. Peças de lata presas com rebites de alumínio.
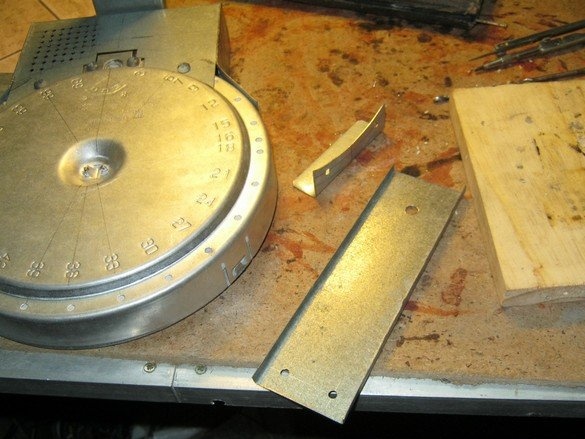
O suporte dianteiro da alça foi montado em uma caixa regular e consiste em duas partes de estanho. É fixado à carcaça com parafusos auto-atarraxantes curtos, a conexão entre si é rebitada.
A parte externa.
Um aquecedor de queimador com potência de 1200 W é muito potente para assar copos - a taxa de aquecimento é grande para um volume tão pequeno, o vidro não tem tempo para aquecer uniformemente, a peça de trabalho racha. Para eliminar a desvantagem, a energia do aquecedor teve que ser reduzida - para ativar uma poderosa resistência em série com ele - um aquecedor a óleo com metade da energia. Ao mesmo tempo, no aquecedor do queimador, a queda de tensão é exatamente metade da tensão da rede - 110 volts.
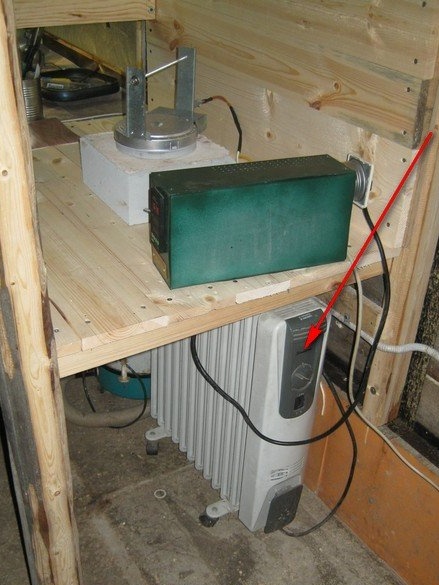
Controlador para controlar o forno. Um soquete para conexão e um bloco de terminais parafusados para o aquecedor do forno estão montados em sua parede traseira. O termopar é conectado diretamente ao controlador.
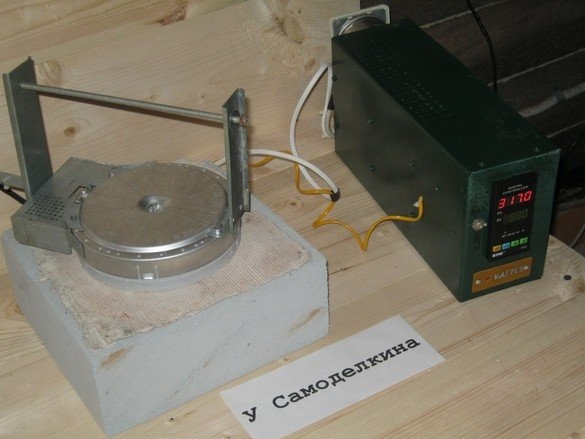
A tampa do forno é refratária - folha de amianto, na qual metade do tijolo é feita de concreto de espuma. Nas proximidades, vale a pena manter o mesmo revestimento resistente ao fogo - nele, se necessário, você pode colocar a ponta quente do forno "aberto".
Sinterização.
Ao sinterizar os vidros, duas temperaturas principais devem ser mantidas - o início da fusão do vidro (710 ... 800 ° C, dependendo do tipo de vidro) e a temperatura de recozimento (500 ... 600 ° C, dependendo do tipo e tamanho da peça). O aquecimento inicial ocorre da maneira mais suave possível (dentro de limites razoáveis, é claro), após o qual a temperatura cai rapidamente para "recozimento".
Normalmente, o processo é controlado por um controlador programável "com perfil térmico". Aqui, um controlador simples é aplicado, mantendo uma temperatura, e eles são trocados manualmente - um dispositivo semiautomático. Ao atingir 800 ° C (~ 30 min.), A tampa do forno está entreaberta, 500 ° C é definido no controlador e o produto é recozido por 1 hora. Depois disso, os aquecedores do forno são desligados e o produto esfria com o forno até a temperatura ambiente (~ 1 hora). Pequenos tamanhos de vidro permitem que você não tenha medo de pequenas imprecisões no processo.
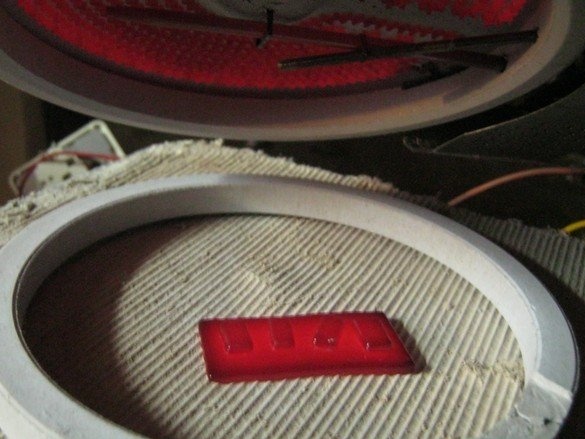
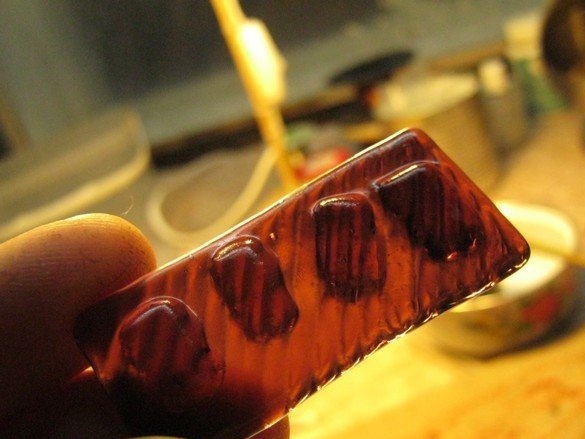
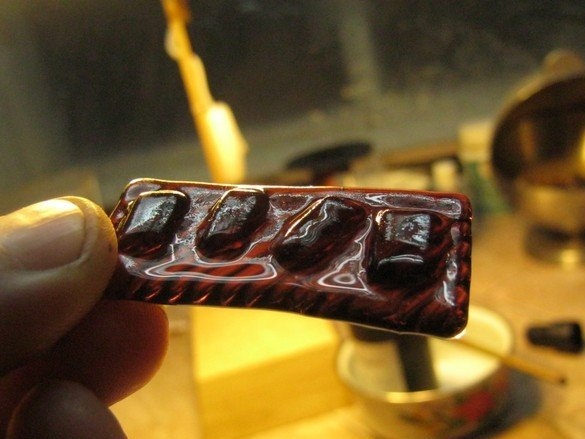
Bem, o primeiro experimento foi bem-sucedido - os óculos se fundiram, mas não em uma superfície plana, a amostra não quebrou - o perfil de temperatura para esse tipo de vidro deve ser considerado bem-sucedido. Vamos tentar ser mais significativos.

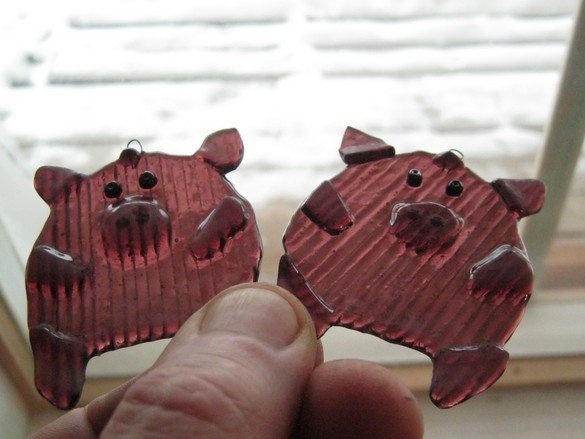

Duas bestas, hmm, bem no espírito do dia, como os ursos olímpicos, ao mesmo tempo ... Aqui, como um experimento, duas variedades de contas foram derretidas, fio de cobre, vidro foi derretido não apenas "colo", mas também praticamente "bunda". Contas (vidro com um KTP diferente) e fio de cobre (ainda mais) devem ser muito pequenas (diâmetro, seção transversal) em relação ao vidro principal, para que as tensões resultantes não destruam o produto.
Babay Mazay, dezembro de 2018