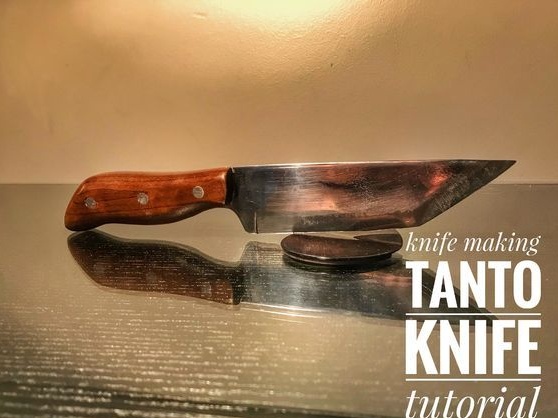
Este estilo de facas como tanto é conhecido por nós no Japão, também é chamado de espada curta. O comprimento da lâmina de uma faca pode variar de 30 a 50 cm e, como regra, a afiação é usada de um lado e, às vezes, de dois.
Por tradição, o metal possui jamon, a alça é removível e também possui uma proteção removível.
Obviamente, a faca feita de acordo com esta instrução tem pouca semelhança com tanto, a lâmina claramente não tem 30 cm, não há jamon e a alça é montada nos pinos. No entanto, a faca mostrou-se bastante boa, apesar do fato de não ter o mesmo nome. No entanto, remotamente, seu perfil lembra um sabre.
Materiais e ferramentas que o autor usou para fazer a faca:
Lista de materiais:
- chapa de aço com alto teor de carbono (isso é precisamente passível de endurecimento);
- madeira para o cabo;
- varetas, rebites de latão (ou outro material para a fabricação de pinos);
- cola epóxi.
Lista de ferramentas:
- ;
- um bom conjunto de lixa;
- papel, lápis, tesoura, acessórios de desenho (para fazer um modelo);
- ;
- cola;
- aguçado;
- lixa de grão diferente;
- uma fonte de alta temperatura (para endurecer) e óleo;
- broca com brocas;
- grampos;
- óleo para impregnação de madeira.
O processo de fazer uma faca:
Primeiro passo Desenhe um perfil e recorte
Primeiro de tudo, você precisa mostrar toda a sua criatividade. É necessário fazer um modelo para a futura faca, isso é feito primeiro no papel. Se desejar, você pode baixar um modelo pronto da Internet e alterá-lo a seu critério.
Em vez de papel, é melhor usar papelão grosso. Quando você recorta o modelo, pode segurar a futura faca nas mãos e garantir que seja conveniente.
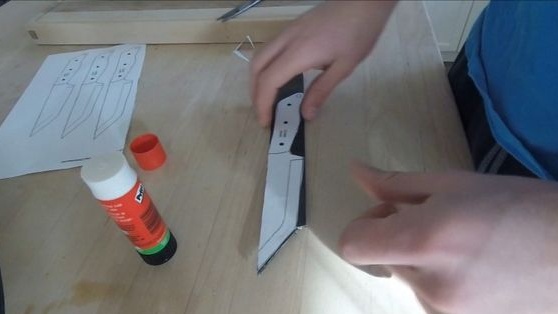
Em seguida, anexe o modelo à peça de trabalho e desenhe um marcador. Agora o modelo pode ser cortado. Para este caso difícil, o autor usa um moedor. Prenda a peça de trabalho com uma pinça ou vício e corte-a lentamente.
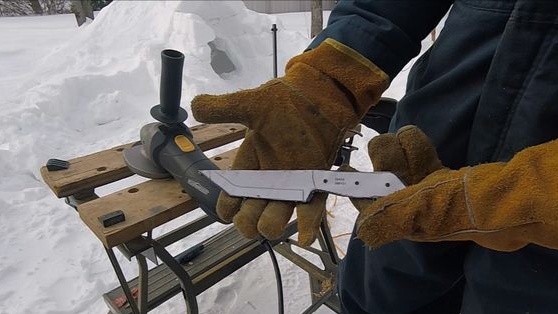
Etapa dois Moer
Após o corte, o perfil será muito rugoso, as bordas serão irregulares, terão entalhes. O perfil ao longo do contorno deve ser levado ao ideal. Para isso, precisamos de um moedor ou um moedor com um disco de moagem. Se houver áreas com problemas no blade, elas poderão ser processadas manualmente usando um arquivo.
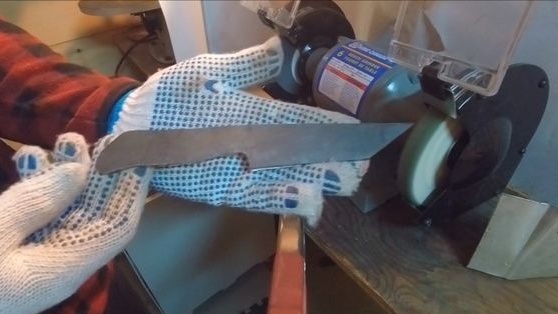
Etapa três Formamos chanfros
Fazer chanfros é um momento crucial, pois as características de corte da faca dependem delas. Quanto maior o chanfro, ou seja, mais suave o ângulo de afiação, mais afiada será a faca e mais fácil será afiada.
Mas existem algumas nuances, uma lâmina fina corta bem, mas não suporta cargas se cortada com uma faca. Então você precisa encontrar um meio termo.
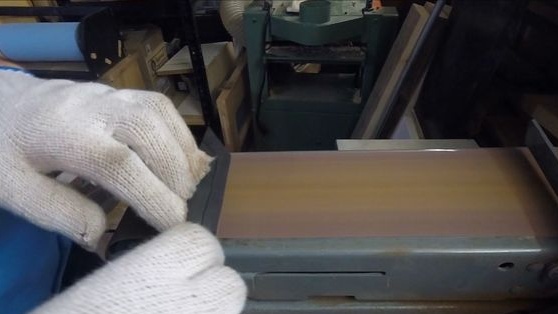
Para tornar os chanfros uniformes e simétricos, primeiro marque tudo. Desenhe uma linha em ambos os lados da lâmina que o chanfro alcançará. Você também precisa dividir a lâmina longitudinalmente em duas partes, para poder ver a linha centralizadora ao retificar. Normalmente, uma broca do mesmo diâmetro que a espessura da peça de trabalho é usada para isso.
Chegando à moagem. Rapidamente e profissionalmente, este trabalho permitirá. Mas nem todo mundo tem esse dispositivo; em casos extremos, você precisará de um moedor com um disco de moagem. Prendemos a peça de trabalho com uma pinça e procedemos à retificação.
Alguns artesãos formam chanfros excelentes usando arquivos comuns. Mas tudo isso é trabalhoso e requer experiência.
Etapa quatro Moagem de metal
Agora vamos começar a triturar metais, aqui você precisaria novamente de uma lixadeira. Se não for esse o caso, tudo terá que ser feito manualmente. Primeiro, usamos uma lixa grande para nivelar os aviões, limpar a ferrugem e remover outros defeitos. Depois, gradualmente aumentamos o papel de esmeril cada vez menor, e assim sucessivamente até a faca brilhar como um espelho.
Muitos artesãos recomendam molhar a lixa na água, por isso é limpa de lascas.
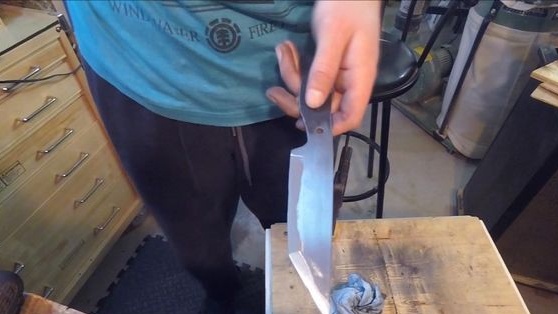
Quinto passo Realizamos furos para os pinos
Certifique-se de concluir esta etapa antes do tratamento térmico, pois será extremamente difícil fazer isso. Além disso, você deve concluir todo o trabalho básico em metal antes de endurecer.
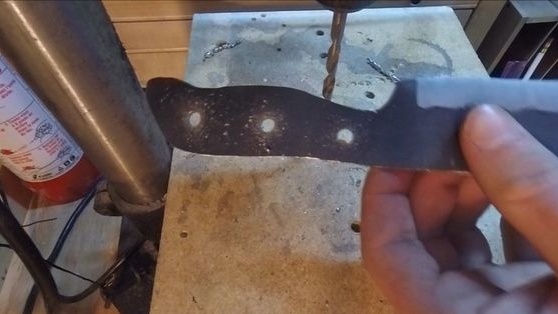
Na peça de trabalho, você precisa fazer dois furos no local onde está a alça. Eles são necessários para instalar os pinos, respectivamente, o diâmetro dos furos é selecionado dependendo da espessura. Pode haver mais pinos, dois são uma opção clássica e isso é suficiente para um conjunto de alça confiável. O autor decidiu fazer três furos na caneta.
Etapa seis Endurecimento de metal
Se você usou aço especial para a fabricação de uma faca, que incorpora uma grande quantidade de carbono, ela pode ser endurecida. Para isso, você precisará de um forno e um ímã permanente. Se você não souber o tipo de aço usado, um ímã permanente ajudará a determinar o grau de aquecimento do endurecimento. Se um ímã é levado ao aço quente e não será atraído, significa que o metal é aquecido até a temperatura desejada.
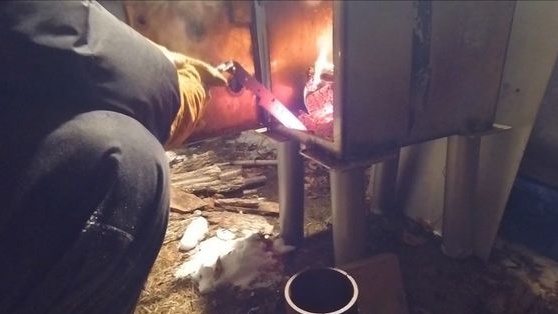
O aço é geralmente aquecido a uma temperatura de 700 a 900 graus. Em princípio, pode ser obtido em um pequeno forno e com a ajuda de carvão. Você precisa encher os carvões com um secador de cabelo, aspirador de pó ou outro dispositivo similar.
Assim que o aço se aquece, é hora de extinguí-lo. Para fazer isso, você precisará de óleo, monomotor ou vegetal. No óleo, o metal não esfria tão rápido quanto na água; portanto, o risco de deformação da pré-forma é reduzido. O autor mergulha o tarugo por 15 segundos, tomando cuidado, pois o óleo inflama e emite um odor forte. Após a têmpera, manuseie a peça com cuidado, pois o metal ficará muito quebradiço.
No final, você precisa fazer a liberação do metal, isso o tornará elástico e a faca não se separará. Se você soltá-lo ou jogá-lo em uma árvore. As férias podem ser feitas em um forno doméstico convencional. Aquecemos a uma temperatura de 200-215 graus Celsius e colocamos a peça de trabalho por uma hora e meia. Depois disso, desligue o forno e deixe esfriar com a faca no estado fechado.
Sétimo passo. Limpeza e polimento de facas
Após o endurecimento, a faca terá escala e traços de óleo queimado. Tudo isso precisa ser limpo. Pegamos uma lixa fina, WD40 ou água comum e procedemos à limpeza. Gradualmente, mude para o menor papel e polir o metal, se desejar.
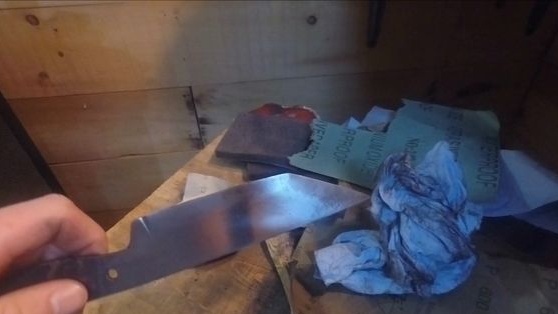
Passo Oito. Montagem da caneta
Agora precisamos fazer espaços em branco para o identificador.Prendemos a faca com a cauda nos adereços e circulamos com um lápis. Cortamos dois espaços em branco com um quebra-cabeças ou outra serra de fita. No entanto, se você não tem um quebra-cabeças, não é assustador, pode cortar os contornos ásperos da alça, mas ela ainda estará retificada. Os tarugos podem ser facilmente girados para o perfil desejado no moedor ou com um arquivo.
No final, você precisa fazer furos para os pinos da árvore, exatamente nesses locais como no metal.
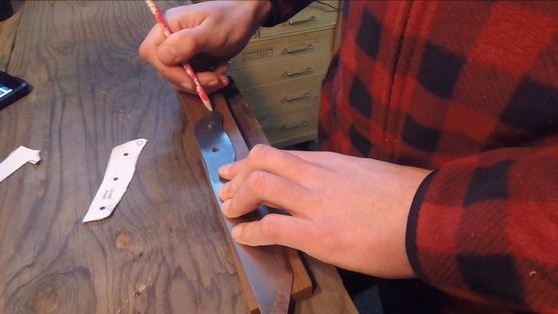
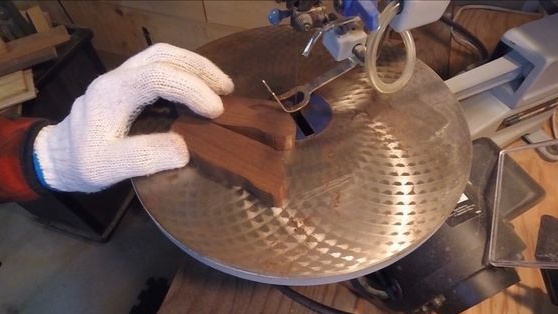
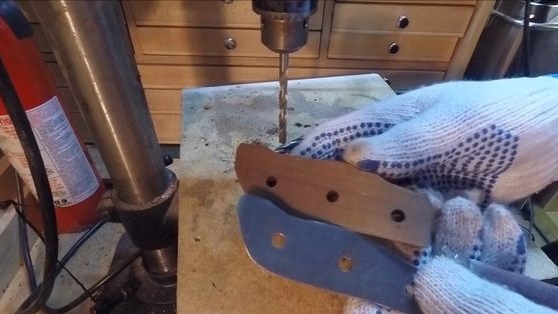
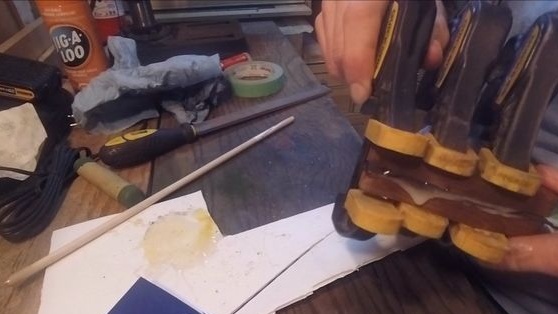
Tomamos cola epóxi e aplicamos na peça de trabalho. Instalamos os pinos e apertamos bem a alça com braçadeiras. Para confiabilidade, o autor usou três peças. Estamos aguardando a cola secar completamente, normalmente leva 24 horas.
Etapa nove. Processamento final
Agora, o passo final permanece, recorremos à ajuda da lixadeira de correia e formamos o perfil final da alça. Se não houver uma máquina de fita, tudo bem, você pode fazê-lo com um moedor, um apontador ou com arquivos comuns.
No final, pegamos uma lixa fina e esmerilhamos bem a superfície da alça, ela precisa ser totalmente lisa.
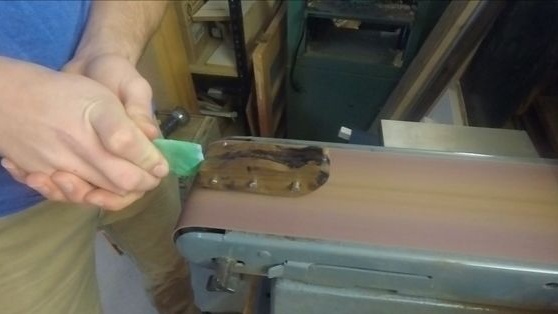
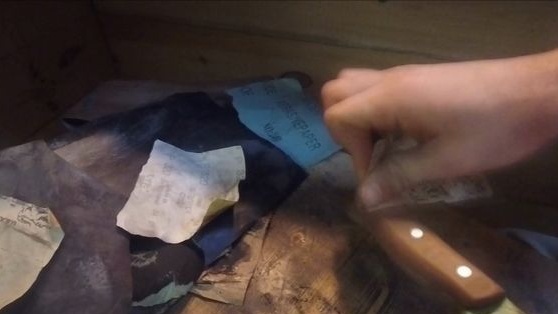
Etapa dez Proteção de árvores
A faca está pronta, agora você deve cuidar para que a madeira não absorva umidade, pois isso rapidamente tornará a faca inutilizável. A madeira é geralmente impregnada com óleo de linhaça, mas existem muitos outros tipos de óleos para trabalhar madeira. No final, polir o cabo com cera de abelha, e não será errado fazer bainha para ele, boa sorte!
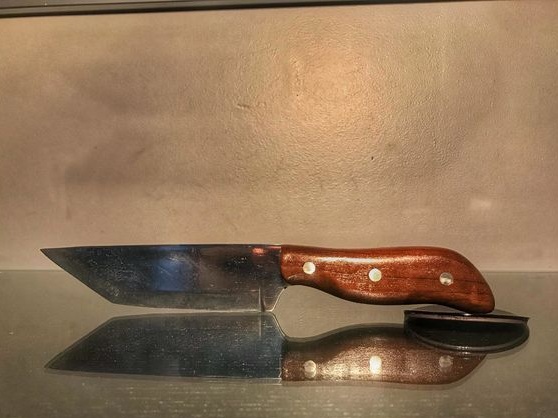