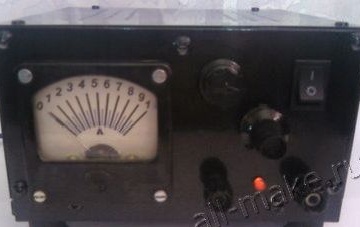
Todo mundo tem um descanso diferente em seu tempo livre. Alguém gosta de deitar no sofá, alguém vai à academia e o autor dessa caseiro, com base em suas necessidades, habilidades e recursos, ele decidiu usar seu tempo livre para criar um novo carregador universal a partir de ferramentas improvisadas que estavam em sua oficina.
Materiais e ferramentas usadas para criar um carregador universal:
caixa de uma fonte de alimentação do computador
broca
linha
marcador
Fio PDDSKT 1,6 mm de diâmetro
fio de cobre com diâmetro de 2,2 mm
resina epóxi
voltímetro
impressora para imprimir amperímetro
transformador da série TS-180
tiristor KU202N
pasta térmica
um par de radiadores
transistores kt315, kt361
primer para metal
Resistor variável de 33 kΩ
folha de fibra de vidro dupla face
-paint
Vamos considerar com mais detalhes a descrição do dispositivo criado e as etapas de sua montagem.
O principal objetivo do trabalho caseiro era a ideia de criar um carregador universal, ou seja, aquele que pudesse carregar quase todas as baterias disponíveis no domicílio: de pequenas baterias de microcádmio digital a enormes baterias automotivas de chumbo-ácido. Naturalmente, a idéia de um dispositivo desse tipo está longe de ser nova, e existem muitos esquemas diferentes para sua criação, um dos quais o autor decidiu trazer à vida em um de seus dias livres.
Assim, decidiu-se fazer um carregador simples, mas universal, cuja corrente de carga pode ser ajustada continuamente dos valores mais baixos ao máximo exigido em 10A, o que será limitado apenas pela tensão disponível na saída do transformador.
Etapa 1: preparar a caixa do dispositivo.
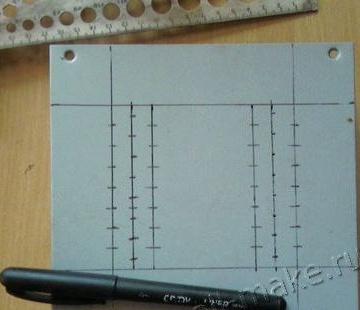
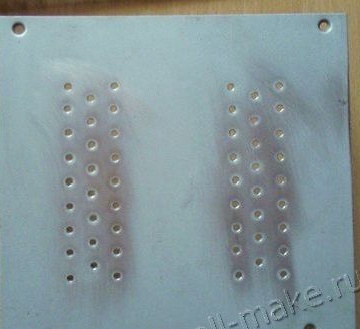
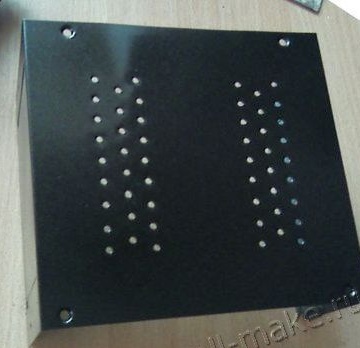
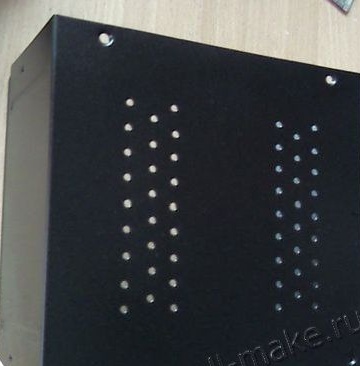
Para começar, a fonte de alimentação foi retirada de um computador estacionário que, após várias alterações, precisaria acomodar todos os elementos de um futuro carregador. Foi completamente desmontado e todas as peças disponíveis foram removidas. Em seguida, o autor limpou a sujeira existente e descobriu como colocar os elementos básicos necessários para um futuro carregador.
Para permitir a circulação de ar no interior do gabinete para resfriar os elementos de aquecimento do dispositivo, foi decidido fazer vários furos na parte superior do gabinete. Primeiro, para isso, a marcação foi feita usando uma régua e um marcador, uma vez que o autor queria obter a aparência do dispositivo de fábrica, para que tudo fosse feito da maneira mais correta e uniforme possível. Depois disso, foram feitas duas fileiras de pequenos orifícios usando a marcação com uma broca.
Como o dispositivo será universal, ele terá vários reguladores e uma balança com um amperímetro, que serão exibidos melhor em um painel frontal do dispositivo. Portanto, com a ajuda da mesma broca, além de arquivos e outras ferramentas que estavam à mão do autor, a frente do caso foi preparada para a futura retirada dos reguladores.
Um radiador será instalado no painel traseiro, portanto também foi modificado.
Etapa 2: fazer um amperímetro.
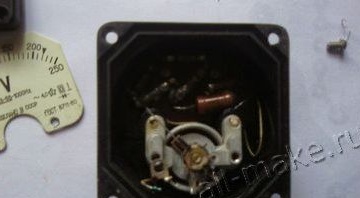
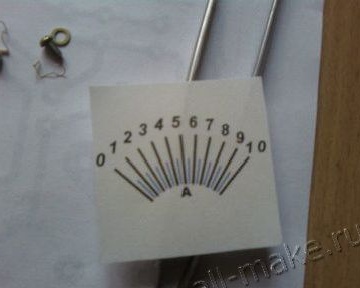
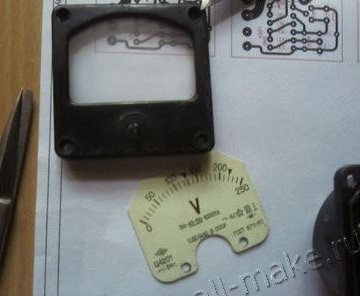
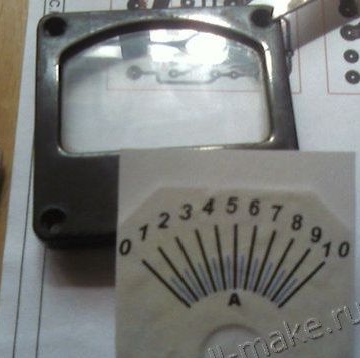
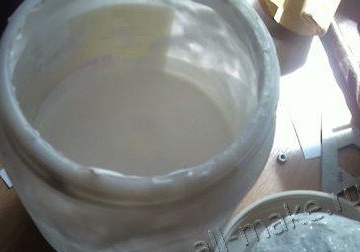
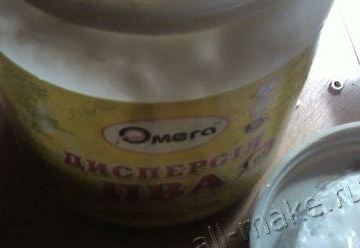

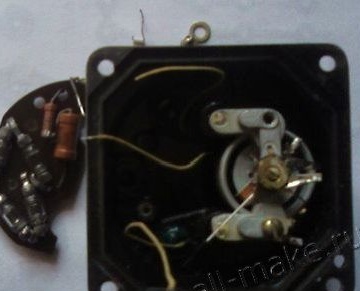
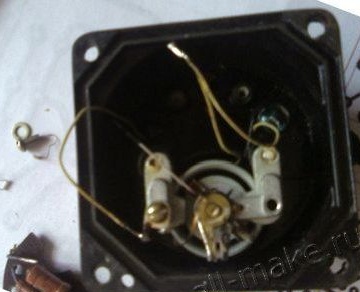
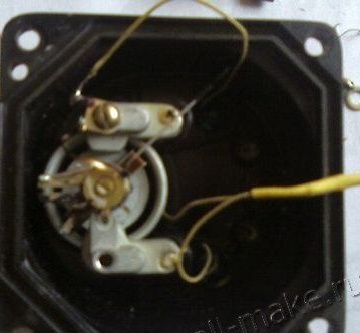
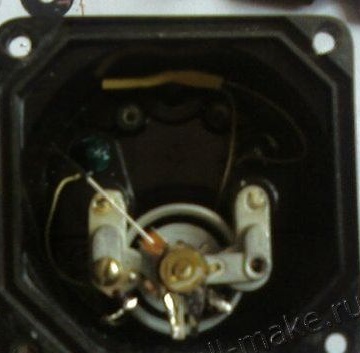
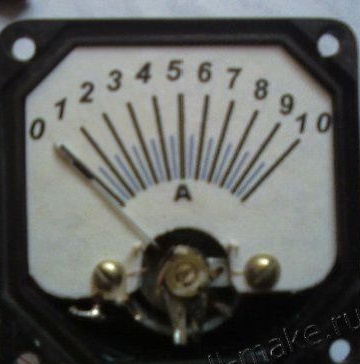
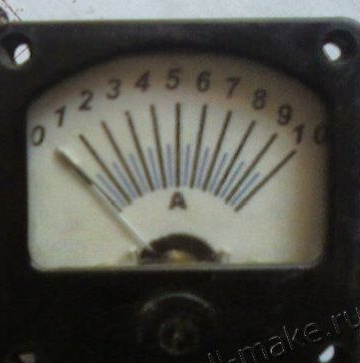
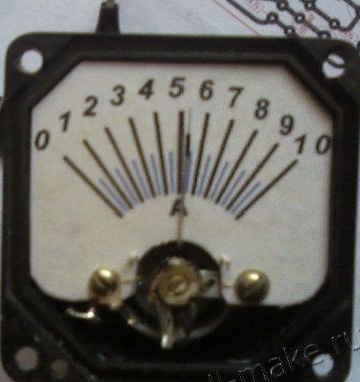
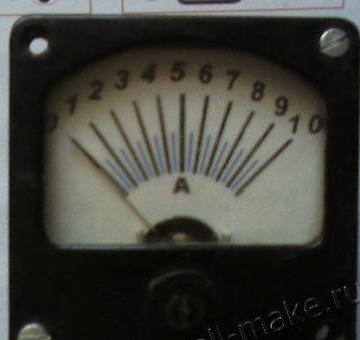
Para poder ver as leituras do carregador, foi decidido conectar um amperímetro diretamente a ele. Porém, como não havia um amperímetro adequado entre os materiais disponíveis, o autor decidiu fabricá-lo a partir de um voltímetro antigo de 250 V, uma vez que possui uma escala linear; portanto, seria um bom ajuste para este dispositivo. Durante a modificação, resistores adicionais e um retificador foram removidos, e as conclusões foram simplesmente soldadas aos terminais. A escala foi desenhada no programa Front designer, após o qual foi impressa por uma impressora e colada na antiga escala do voltímetro.
O fio PDSKT encontrado na oficina tinha 2,15 m de comprimento e 1,6 mm de diâmetro e foi usado como derivação para um amperímetro. Este fio foi enrolado em torno da estrutura, após o qual foi fixado com fios e preenchido com resina epóxi, fixando assim a estrutura com segurança. Considerando que isso é suficiente, e uma diferença nas leituras de 5% não afetará significativamente a operação do dispositivo, ele passou para o próximo estágio de criação de um carregador.
Etapa três: preparação e colocação dos principais elementos do carregador na carcaça.
Quando as etapas preparatórias foram concluídas, o autor passou a colocar os elementos básicos dentro do dispositivo. Para começar, ele começou a refazer o transformador existente em 27 V. Ele foi enrolado com um fio de cobre com um diâmetro de 2,2 mm, embora 1,6 mm ou um barramento com uma área de cerca de 4 mm quadrado tivesse subido. Depois disso, ele foi colocado no interior já com tensão de 18 V no enrolamento secundário e com uma potência de 120 watts ou mais.
Um radiador foi instalado em toda a área da parede traseira, que consiste em duas partes conectadas por pasta térmica. Um tiristor KU202N com capacidade de 10 A. foi anexado a este radiador.Além disso, uma ponte de diodo 35 A foi conectada ao mesmo radiador montado.
Para construir o regulador de corrente, o autor usou um gerador de pulsos montado a partir dos transistores CT-315 e CT-361, embora outros com tensão de 30 V e ganho de mais de 100. Uma nuance importante é que, se você usar transistores com uma grande dispersão, então em pequenas correntes podem ser interrompidas na geração, por isso é melhor usar ambos os transistores com ganho próximo, mas com condutividade diferente.
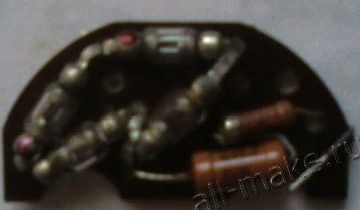
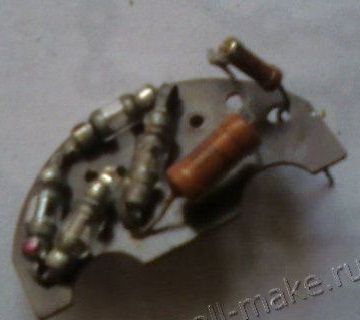
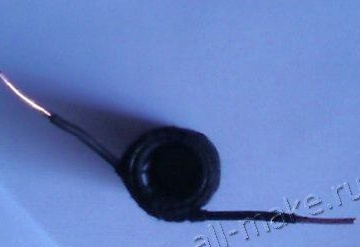
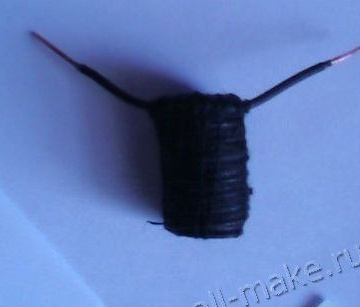
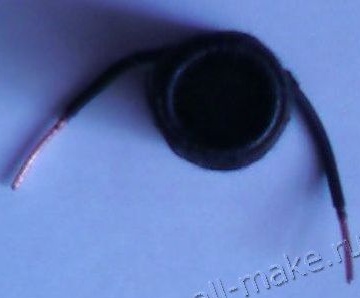
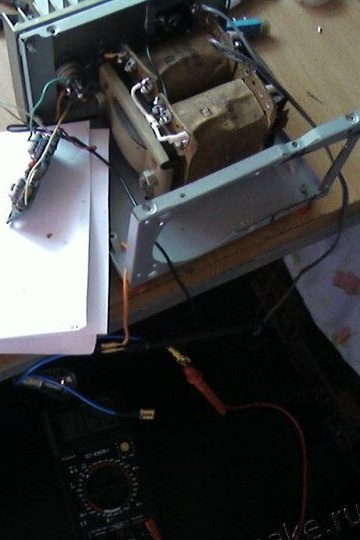
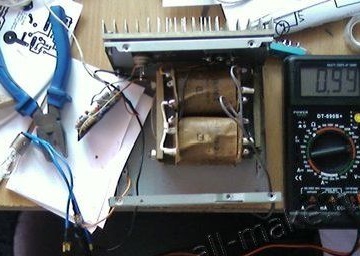
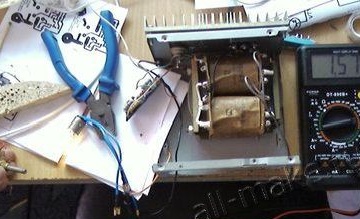
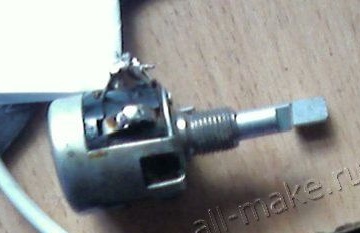
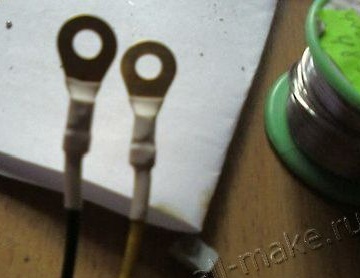
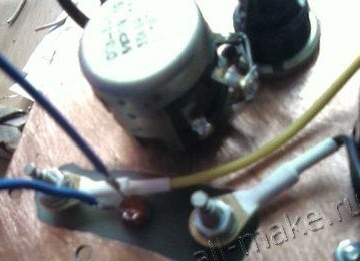
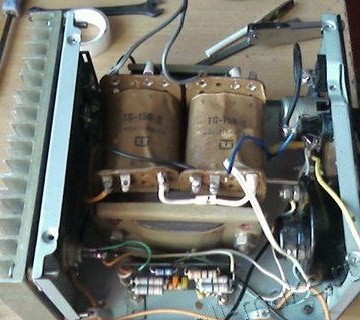
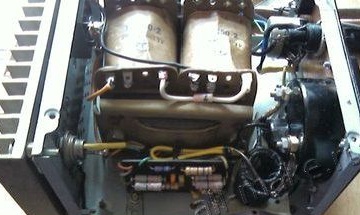
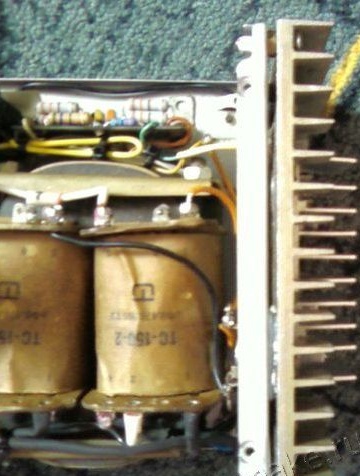
O resistor de variável dupla disponível com uma resistência de 33 kOhm também foi modificado para criar um regulador de carregador. Para diminuir o limiar para 0,5 V, o autor fez um paralelo com o resistor e foi obtido um valor de resistência de 16,5 kOhm, respectivamente. Tudo isso foi feito para uma faixa maior e, consequentemente, para uma maior universalidade do carregador resultante; portanto, se fosse necessário carregar baterias de 12V de carro, um resistor variável de 4,7 kΩ teria surgido, mas o autor decidiu se concentrar na versatilidade do dispositivo.
Etapa quatro: criar um esquema.
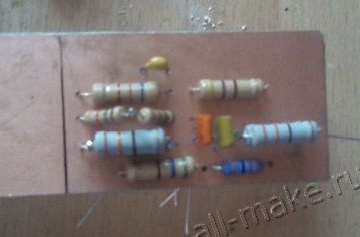
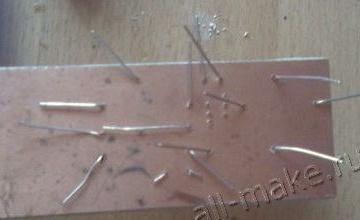
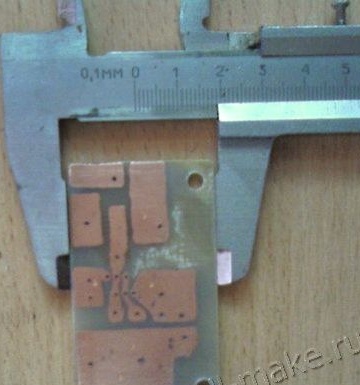
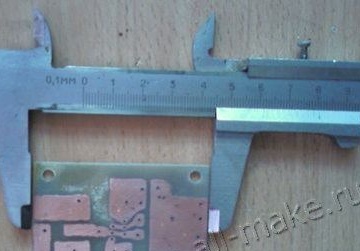
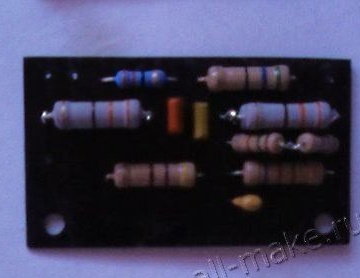
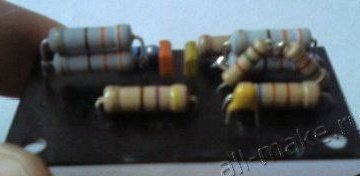
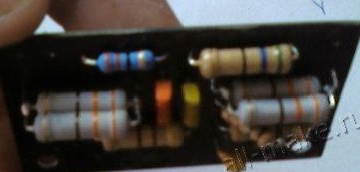
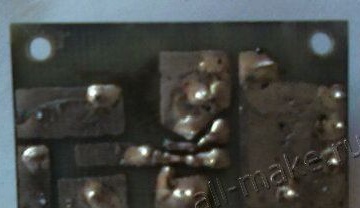
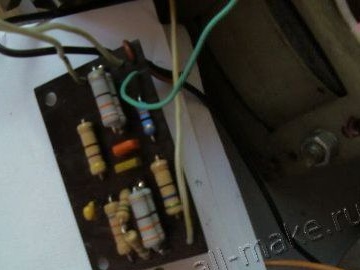
Como as dimensões do gabinete usado são limitadas, para criar o circuito, o autor decidiu usar uma placa de circuito impresso, embora possa ser feita com uma instalação articulada.
O autor também fez a placa de circuito para si a partir dos meios disponíveis. Demorou cerca de meia hora para gravá-lo, após o qual foi lavado, e o autor passou a soldar, estanhar e, posteriormente, instalá-lo no estojo do dispositivo.
Quinta etapa: criando um painel frontal para regular o carregador e a pintura.
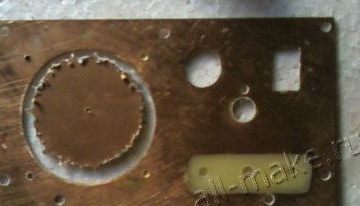
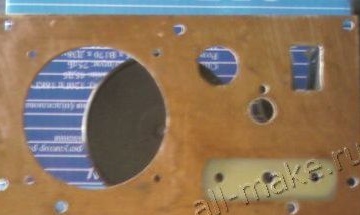
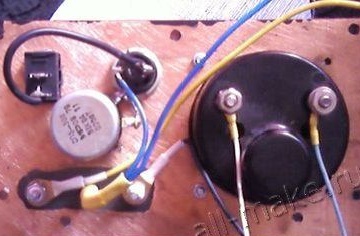
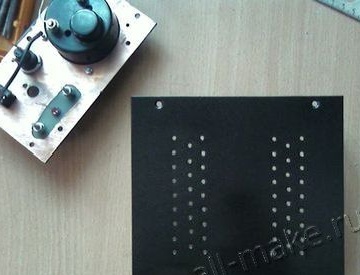
Como material do painel frontal, o autor escolheu fibra de vidro. Foi gravado em ambos os lados nos terminais. Além disso, de acordo com as marcações marcadas, foram cortados orifícios para fixar e instalar blocos de terminais, indicadores, reguladores, um interruptor, um fusível e uma escala de amperímetro.
Depois disso, o painel resultante foi anexado ao corpo principal com parafusos autorroscantes e todos os controles foram retirados e fixados nos orifícios correspondentes.
Em seguida, pegando a tinta metálica preta que o autor havia deixado depois de pintar o para-choque do carro, ele a usou para pintar todo o corpo do carregador resultante.
Você pode ver o resultado nas fotografias, o dispositivo tem uma aparência muito agradável e parece que foi montado em alguma empresa, e não em a garagem.
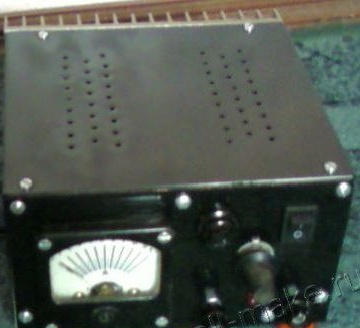
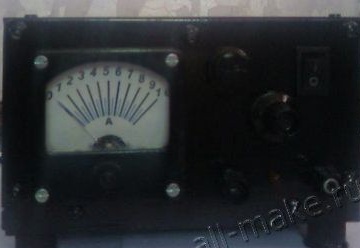
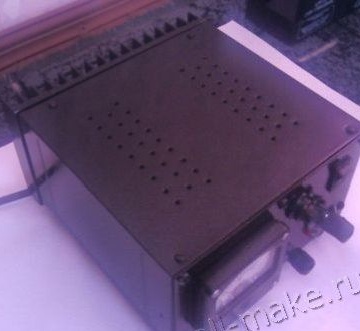
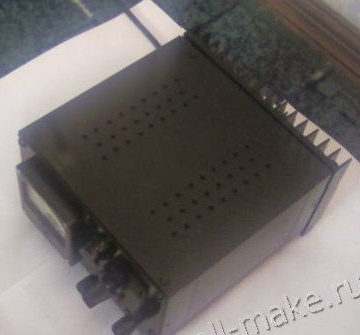
Etapa seis: indicações de teste.
O dispositivo foi ligado à noite para carregar uma bateria 6ST90. A bateria foi carregada por cerca de 12 horas com uma corrente de carregamento de 8A. Nenhuma avaria ou mau funcionamento foi detectada sob essa carga. O aquecimento era pequeno, devido à boa transferência de calor e transferência de calor dos radiadores, o transformador não era muito aquecido. Daí resulta que este carregador é totalmente funcional e confiável.
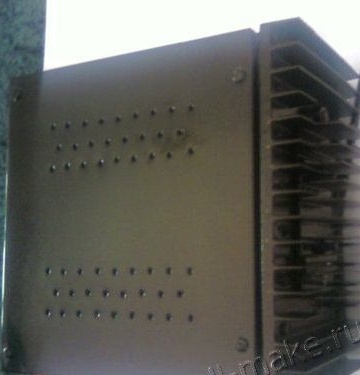
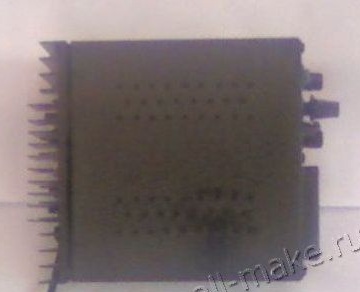
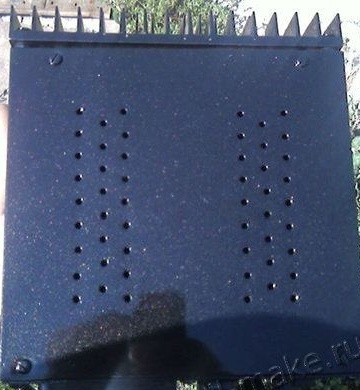
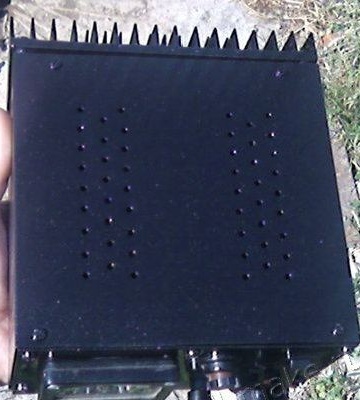
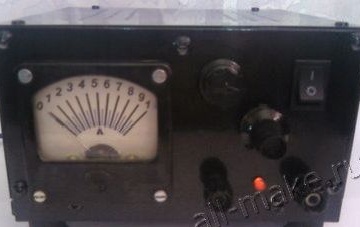
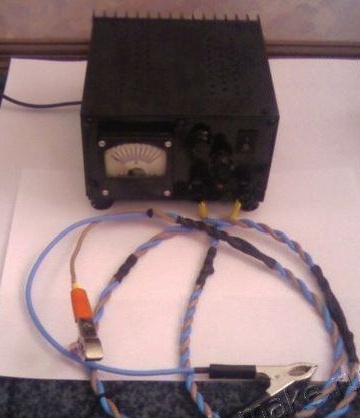
Você pode encontrar informações adicionais no link "fonte" abaixo, onde também pode fazer perguntas ao autor deste dispositivo.